Меню
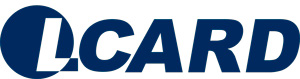
+7 (495) 785-95-25
sale@lcard.ru
sale@lcard.ru
На сегодняшний день при строительстве и реконструкции железнодорожных магистралей осуществляется укладка бесстыковых путей. Это вызвано общей тенденцией роста скорости подвижного состава, особенно скоростных пассажирских поездов, увеличенной интенсивностью движения и грузонапряженностью. Авторы статьи [1] также отмечают, что современные высокопрочные рельсовые стали требуют специальные режимы сварки и технологические средства, без которых невозможно обеспечить гарантированную целостность и качество сварного соединения. Одним из таких средств является термическая обработка (ТО) сварного соединения рельсов, которая минимизирует последствия высокотемпературного нагрева металла в процессе сварки, измельчает его микроструктуру, повышает прочность сварного соединения, снимает остаточные напряжения.
Целью и задачей данного исследования является разработка математической модели для численного моделирования процесса высокочастотной индукционной ТО модельного образца, а также модель определенного параметра пространственно-временного распределения температурного поля в процессе выполнения ТО. При этом для уменьшения времени расчета процесс математического моделирования целесообразно разделить на два этапа: первый – моделирование процесса высокочастотного индукционного нагрева системы "индуктор – изделие"; второй – моделирование структуры фазовых превращений и свойств металла шва в изделии в зависимости от термического цикла.
Далее мы остановимся только на проведённых авторами экспериментах по физическому моделированию процесса индукционной ТО. Физическое моделирование происходило на образце, вырезанном из головки железнодорожного рельса из высокопрочной рельсовой стали К76Ф со сварным соединением, находящимся по центру образца (рисунок 1,а).
Рисунок 1. Образец для физического моделирования индукционной ТО: а – иллюстрация схемы вырезки модельных образцов из сварного соединения железнодорожного рельса; б – расположение точек контроля температуры модельного образца.
Для индукционного нагрева модельного образца использовался разработанный маломощный лабораторный макет высокочастотного источника питания на базе мостового инвертора. Резонансный колебательный контур лабораторного макета работает по последовательному типу подключения RLC‑круга, где нагрузкой является опытный модельный образец. Медный трёхвитковый водоохлаждаемый индуктор с концентратором магнитного поля расположен над зоной сварного соединения. Подключена батарея компенсирующих емкостей и согласующий трансформатор. Для контроля силы тока индуктора, частоты, формы и амплитуды напряжения на индукторе использовался пояс Роговского и цифровой осциллограф Siglent SDS 1102CML+. Для контроля изменения температуры в модельном образце были определены две контрольные точки, первая – термопара 1 (рисунок 1) в центральной части образца на его поверхности для определения максимальной температуры нагрева образца, и вторая – термопара 2 на конце зоны термического воздействия сварного соединения для контроля распространение температурного поля в соответствии с математическим моделированием. В качестве датчиков температуры использовали хромель-алюмелевые термопары типа К, которые приваривались в определенные места на поверхности образца посредством конденсаторной сварки.
Преобразование сигнала из термопарных датчиков в реальном времени производилось посредством модуля АЦП E20‑10 с применением блока гальванической развязки Promsad PSA0101 и специального ПО для визуализации полученных данных на компьютере. При проведении экспериментов по физическому моделированию индукционной ТО опытного модельного образца из высокопрочной рельсовой стали был получен термический цикл процесса индукционного нагрева (рисунок 2).
Рисунок 2. Изменение температур во времени в контрольных точках модельного образца: 1, 2 – термический цикл в процессе физического моделирования; 1', 2' – расчетные данные математического моделирования.
При сравнении расчетных и экспериментальных термических циклов наибольшая погрешность составила около 10 %. Из полученных расчетных данных при использовании метода конечных элементов и измеренных данных при физическом моделировании термических циклов можно заключить, что расчетное изменение температуры в математической модели хорошо согласуется с экспериментальными данными. Это даёт возможность применять её для следующего этапа моделирования – определения структурных преобразований в металле сварного соединения при воздействии технологических параметров термической обработки, что позволяет оптимизировать технологические процессы индукционной термической обработки сварных стыков железнодорожных рельсов.
Источник:
Губатюк Р.С., Римар С.В., Прокоф’єв О.С., Костін В.А., Дідковський О.В., Антіпін Є.В. Моделювання процесу індукційної термічної обробки зварних з’єднань з рейкових високоміцних сталей // Автоматичне зварювання. – 2021. – № 9. – с. 43‑54.
Адрес: 117105, Москва, Варшавское шоссе, д. 5, корп. 4
Многоканальный телефон:
+7 (495) 785-95-25
Отдел продаж: sale@lcard.ru
Техническая поддержка: support@lcard.ru
Время работы: с 9-00 до 19-00 мск